Q&A
April 04, 2025
An Interview with Jeff Clement & Bill Welch: Parenteral Manufacturing and Packaging Trends
An Interview with Jeff Clement & Bill Welch
How are emerging technologies like AI and continuous manufacturing reshaping the landscape of parenteral drug production, and what challenges do companies face in implementing these innovations?
Jeff Clement: Contract development and manufacturing organizations (CDMOs) are at the forefront of integrating artificial intelligence (AI) and continuous manufacturing to enhance efficiency, scalability, and compliance in parenteral drug production. AI-driven automation allows CDMOs to optimize formulation development, enhance real-time process monitoring, and improve predictive maintenance, ultimately reducing batch failures and ensuring consistent product quality. Similarly, continuous manufacturing streamlines production, eliminating batch-to-batch variability and enabling rapid response to fluctuating client demands. These innovations enhance speed-to-market while maintaining stringent regulatory and quality standards.
However, CDMOs face distinct challenges when implementing these technologies. The transition from batch to continuous processing requires significant capital investment, which must be balanced against the diverse and evolving needs of multiple product classes – each with its unique setup challenges. Regulatory uncertainty further complicates adoption, as global agencies continue to refine guidelines for AI-driven and continuous manufacturing processes. Additionally, CDMOs must invest in workforce training and digital infrastructure to fully leverage AI-powered analytics while ensuring robust data security measures.
With the increasing focus on biologics and personalized medicine, how are parenteral packaging solutions evolving to meet the demands for more specialized and sensitive drug formulations?
Bill Welch: The rise of biologics and personalized medicine is driving significant advancements in parenteral packaging solutions to ensure stability, sterility, and patient-centric delivery. Given the sensitivity of biological formulations, packaging materials, and container closure systems must minimize interactions that could compromise drug 56 | | March 2025 APR_March2025.indd 56 integrity. Care must be given at an early stage to consider not only scalability for a clinical product progressing to commercial volume but compatibility with a drug product’s chosen container closure to best ensure a seamless transition to the intended drug device delivery system.
Prefilled syringes (PFS), autoinjectors, and cartridges with pens are gaining traction as preferred delivery systems, catering to the rising demand for self-administration and patient convenience. These formats not only enhance dosing accuracy and reduce manufacturing API loss but also mitigate contamination risks.
Addressing the growing complexities of drug formulations, particularly in terms of volume and viscosity, there is increasing focus on on-body injectors as a novel approach for subcutaneous delivery of biologics. Supported by human factors studies in certain patient populations, the range of autoinjector applications continues to expand; this demonstrates the feasibility of these higher volumes and viscosities, providing additional patient-centric drug delivery options for improved health outcomes.
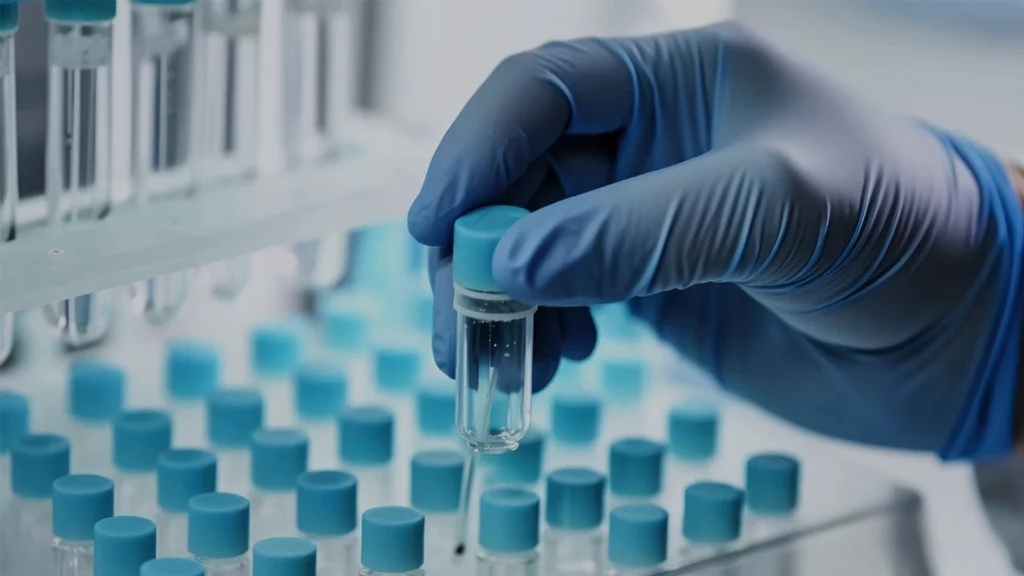
What strategies are manufacturers employing to address the ongoing issues of drug shortages and supply chain disruptions in the parenteral drug market?
Jeff Clement: CDMOs play a critical role in addressing drug shortages and supply chain disruptions in the parenteral drug market through strategic investments and operational agility. To enhance supply chain resilience, CDMOs are increasingly diversifying supplier networks, sourcing raw materials from multiple geographic regions, and forging strategic partnerships to mitigate risks associated with single-source dependencies.
Recent events have shone a spotlight on the need for secure and nimble supply chains. Biopharmaceutical companies seek service providers who can provide integrated solutions to support drug products through all development lifecycles and into commercialization. This turnkey, “under one corporate roof” approach mitigates the need to transfer between suppliers and, as such, reduces supply chain complexity and risk.
Considering this, multi-product manufacturing and device-agnostic packaging facilities provide flexible solutions that allow CDMOs to pivot between various drug formulations and delivery systems with minimal downtime. CDMOs with global facilities not only support worldwide supply with a local presence but also provide business continuity options to mitigate risk against unforeseen supply chain disruptions.
Given the ever-increasing value of many medicines –particularly those treating rare diseases and indications such as oncology – operational and supply chain flexibility allows companies to manage effectively through difficult-to-predict supply dynamics. One such supply chain safeguarding strategy that our client partners utilize is dual sourcing, which can entail dual market supply, scale-up to address the increase in demand, and capacity reservation models to secure back-up supply as needed, among other risk mitigation tactics.
Regulatory engagement is another key strategy, as CDMOs work closely with health authorities to expedite approvals for alternative raw materials or manufacturing sites during supply crises.
How are regulatory changes, such as the European Medical Device Regulation (MDR) Annex 1, impacting parenteral drug manufacturing and packaging processes, and what steps are companies taking to ensure compliance?
Jeff Clement: EudraLex Volume 4 Annex 1 of the EU Good Manufacturing Practice (GMP) guidelines outlines requirements for sterile medicinal products. The revision of Annex 1, which became effective in August 2023, focuses on addressing new technologies and concepts, including Pre-Use Post Sterilization Integrity Testing (PUPSIT), the use of closed systems (RABS and isolators), and automation. It also reinforces quality risk management principles, as well as the requirement for contamination control strategies to ensure patient safety.
As a leading CDMO, PCI is proactively adapting to these regulatory shifts through several key initiatives. First, we are continuing to invest in state-of-the-art aseptic processing technologies – including isolators, automated filling systems, and advanced environmental monitoring solutions – to align with Annex 1’s heightened sterility assurance requirements.
Second, we reinforce our quality management systems through a risk-based approach to contamination control strategies (CCS). This includes implementing real-time monitoring, data-driven process validation, and enhanced personnel training to meet regulatory expectations.
Third, we collaborate closely with regulatory authorities and industry partners to ensure alignment with evolving compliance standards. Regular audits, proactive gap assessments, and continuous process optimization allow us to maintain adherence to global GMP requirements while ensuring manufacturing efficiency.
By integrating these measures, CDMOs play a critical role in supporting pharmaceutical companies in achieving compliance, minimizing supply disruptions, and maintaining the highest standards of product safety for parenteral drugs.
Looking ahead what do you foresee as the most significant trends and challenges in parenteral drug manufacturing and packaging?
Bill Welch: The parenteral drug market is evolving rapidly, driven by technological advancements, regulatory changes, and shifting market demands. Looking ahead, several key trends and challenges will shape parenteral drug manufacturing and packaging.
- Automation and Robotics: Increasing adoption of advanced aseptic processing technologies, including isolators, robotics, and closed-system manufacturing, will further enhance sterility assurance and regulatory compliance. These innovations help mitigate contamination risks, protect operators, and improve operational efficiency.
- Orphan Drugs and Personalized Medicine: The rise of personalized medicines and orphan drugs necessitates flexible small-batch manufacturing solutions, such as modular facilities and single-use technologies. These approaches enable rapid scalability and production adaptability for complex biological therapies.
- Patient-Centricity & Self-Administration: There is a noticeable move towards advanced drug delivery and drug-device combination products, with parallel development studies and prefilled syringes being introduced earlier in clinical trials to develop drug product presentations in their intended commercially viable devices, such as autoinjectors or pens.
- Sustainability: As many geographies increasingly embrace environmentally responsible practices, manufacturers face the challenge of creating eco-friendly solutions while maintaining product safety and effectiveness. By assessing the lifecycles of products in their entirety – from device component materials and packaging substrates to storage and final end-user distribution – companies can identify key areas for high-impact sustainability improvements.
However, these advancements come with challenges. Supply chain vulnerabilities remain a pressing concern, requiring manufacturers to implement diversification strategies and predictive analytics to prevent disruptions. Additionally, evolving global regulatory requirements, such as the EU MDR Annex 1 and the FDA’s evolving guidance, necessitate continuous investment in compliance and quality assurance.
It is an exciting time in the industry, as the enhanced prioritization of making drug delivery more conducive to patient lifestyles and experiences is an overdue and potentially game-changing effort. By proactively addressing these challenges and embracing innovation, CDMOs will play a pivotal role in ensuring a resilient, efficient, and patient-centric parenteral drug supply chain.
Published in Women American Pharmaceutical Review, April 2025
We are committed to supporting clients at every stage of the manufacturing cycle, delivering best-in-class services efficiently and effectively.
Find out more about our fully integrated Packaging Services.