As a leading global lyophilization CDMO, PCI Pharma Services is an expert and innovator offering one of the largest lyophilization capacities in the industry.
With over 25 years of experience, we have the scientific expertise, global facilities, and scalable equipment to help our clients achieve success. We are uniquely positioned to develop lyophilization cycles from the beginning or to optimize existing cycles, providing a commercially desirable yet economical process. Having developed over 675 lyophilization cycles, client partners rely on us to achieve their Quality Target Product Profile and deliver life changing therapies to patients.
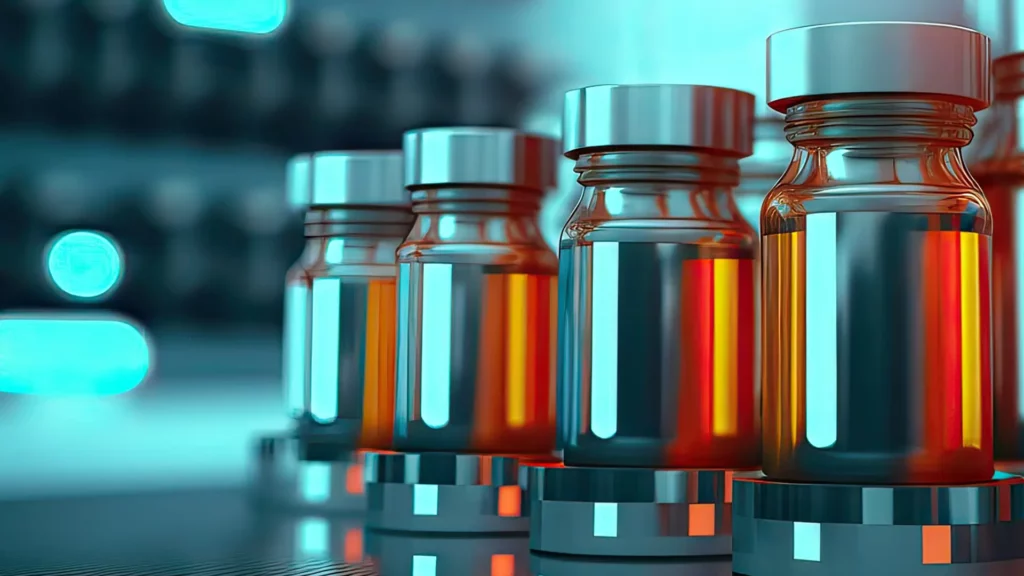
Client Case Study
Client Challenge
A small US-based biotech company approached PCI Pharma Services seeking support for their labile monoclonal antibody drug product. They were still in the preclinical development phase and had determined that the drug product, in its current form, would not be suitable for Phase I clinical trials due to stability issues. They sought an experienced CDMO with scientific expertise to aid further formulation development and a partner with scalable sterile fill-finish and lyophilization solutions to support not only their early phase clinical studies but also future late phase trials and ultimately commercialization.
Process and Solution
PCI worked with the client to develop a strategic three part plan to address not only their short-term objective of advancing their product into the clinic but also to plan for the later stage clinical trial program. The three part development plan consisted of:
- An initial quick start lyophilization program to provide a limited study to conserve the client’s valuable bulk drug substance, expedite time, and reduce costs. Note: This phase appropriate solution would produce a lyophilized product suitable for Phase I trials, although further development would be required if the product advanced in the clinic.
- A formulation development program to enhance overall liquid stability.
- A fully optimized lyophilization cycle to support long-term stability suitable for late stage clinical trials and future commercial manufacturing.
Part One
To address the client’s short-term needs of initiating Phase I trials with a lyophilized presentation of their drug product, PCI developed a plan to analyze the thermal properties of the products’ current liquid formulation, with the aim to design a cycle without the use of additional compounds. Using mDSC and FDM the development team successfully defined and understood the physical characteristics of the formulated product and gained confidence that even in the current state, a cycle could be generated. This helped to guide a limited, data-based study using just two lyophilization runs in the drug product’s current formulation, limiting drug quantity and providing a sufficient design space in which to operate. PCI was able to develop a preliminary lyophilization cycle suitable for Phase I GMP clinical trial manufacturing within an accelerated timeframe of just a few weeks.
Part Two
Following the completion of the GMP clinical trial manufacturing campaign to provide supplies for their First in Human (FIH) clinical trial, the second stage of the program was initiated for future clinical trial supply. During this phase it was agreed upon with the client to undertake a development program for the drug formulation prior to further development of the lyophilization cycle to help gain stability and mitigate elongated cycle times. To maximize the formulation development process, PCI Formulation Development scientists reviewed all pre-formulary data available and developed a plan to evaluate a small number of excipients to further enhance the molecule’s stability and assess a number of cryoprotectants, with success of a lyophilized product in mind. A parallel development path was used to evaluate short term stability of both the liquid and lyophilized presentations of the drug product.
With a view to the long-term cGMP manufacturing costs of the molecule, the various liquid formulations were screened prior to performing further development of the lyophilization cycle. Developing a robust liquid formulation prior to final lyophilization development served several purposes; primarily, having the most stable liquid formulation is beneficial if there are any delays during GMP product manufacturing, or as the program progresses and larger scale batches are needed. The additional liquid stability is required while the product is sterile filtered and filled into vials.
Additionally, as lyophilized drug products are more expensive (often 50 to 70% higher) to manufacture than GMP liquid fill-finish production, developing a more stable liquid formulation of the finished drug product was deemed worth the additional investment in both development costs and time over the lifecycle of the product due to the significant future cost savings that could be achieved. If the product has adequate stability as a liquid presentation, it may be worthwhile to pursue that pathway and during the development phase, the lyophilized dosage stability would then be used as a backup in the case of the liquid formulation not supporting the required stability.
Part Three
In this case, the stability data did not support the case for a liquid presentation, and a lyophilization development and optimization program was initiated. The candidate formulation with the best stability data was selected for further lyophilization development.
The selected formulation was re-analyzed using mDSC and FDM to understand the thermal profile of the product and subsequently, a series of iterative lyophilization development runs were conducted and evaluated against the agreed upon CQAs, including cake appearance, reconstitution time, moisture content, and assayed using HPLC. As the lyophilization cycle parameters were nearing completion, a cycle optimization program was initiated. During the optimization phase of the program, a ‘sample thief’ was used to collect numerous samples during the secondary drying to map moisture content and residual solvents in real time. This established an efficient secondary drying cycle and fully characterized the design space of acceptable lyophilization process parameters. This provided for the development of a robust and efficient lyophilization cycle, saving significant long-term manufacturing costs.
To ensure a commercially robust lyophilization process, reduce the risk of collapse and safeguard that the finished product consistently met the finished product CQAs at release, PCI’s expert Process Development team continued to characterize the formulation by performing “Intentional Collapse Studies” (ICS) during the final stages of lyophilization development. This intentional collapse of the product allowed the team to fully understand the potential points of failure and verified that macro-collapse does occur in the final vial presentation where the FDM and DSC testing data indicated.
Throughout the course of the client’s clinical development journey, our experienced Process Development team maintained focus on the future and planned for long-term success, delivering a robust lyophilization cycle with parameters that were transferable to any large-scale clinical/commercial freeze-dryer to support commercialization.
At PCI, together with providing science driven, flexible scalable solutions, delivering best-in-class services efficiently and effectively, we are committed to meeting the dynamic needs of our client’s drug product journey. We immerse ourselves in every client project, working in partnership to provide collaborative, creative and tailored approaches to deliver upon our purpose of bringing life changing therapies and patients.
To download this case study: Client Case Study: The Future of Lyophilization and Choosing a CDMO Partner (PDF)
We are committed to supporting clients at every stage of the manufacturing cycle, delivering best-in-class services efficiently and effectively.
Find out more about our Lyophilization Cycle Development Services.