Article
May 02, 2025
The Future of Pharmaceutical Packaging: The Basics and Benefits of Late Stage Customization
The pharmaceutical industry is facing an evolving landscape of challenges and opportunities, with supply chain complexities, personalized medicine, and shorter product lifecycles becoming the new norm.
In the past, we’ve seen a lot of products introduced to the market that require large-scale production lines. We’re now seeing a shift to more specialized medicines where large-scale production is not the best option as it could lead to higher costs and more waste. One innovative approach that addresses these challenges is Late Stage Customization (LSC), a method that enables companies to efficiently package products in a more flexible and responsive manner that increases speed to market.
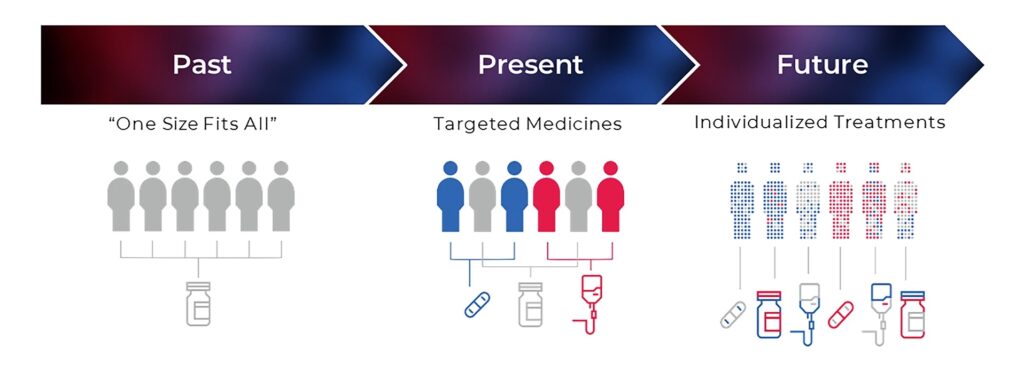
Understanding Late Stage Customization
Late Stage Customization is a digital printing-based approach that allows pharmaceutical companies to delay the final packaging customization of their products until the latest possible moment. This process helps manufacturers and contract packaging organizations (CPOs) efficiently respond to market demands, regulatory requirements, and evolving patient needs. Instead of printing large batches of pre-configured packaging, companies can maintain a standardized stock and personalize packaging based on real-time requirements.
Traditionally, pharmaceutical packaging follows a linear model: bulk drug production, packaging, and distribution. However, as personalized medicine, gene therapies, and region-specific regulatory compliance become more prevalent, this model often leads to high costs, wastage, and inefficiencies. Late Stage Customization offers a more dynamic, on-demand solution that benefits both manufacturers and patients.
The Trumpet Syndrome: Managing Lead Time vs. Complexity
One of the most significant bottlenecks in pharmaceutical packaging is what industry experts refer to as the “Trumpet Syndrome.” The lead time for API or drug substance can be extremely long and narrow, but then gets converted into drug product and from there into a dosage forms. While supply chain complexity may be minimal at the early stages of manufacturing, complexity increases as the process moves downstream to commercial packaging, where companies are met with multiple SKUs, regulatory requirements, and varied dosage forms. Managing this growing complexity within short lead times is a challenge that LSC is uniquely positioned to solve.
By postponing customization to the final stage, manufacturers can simplify bulk production while ensuring that market and patient-specific packaging is applied only when necessary. This not only reduces production waste but also enables companies to maintain flexibility in their operations.
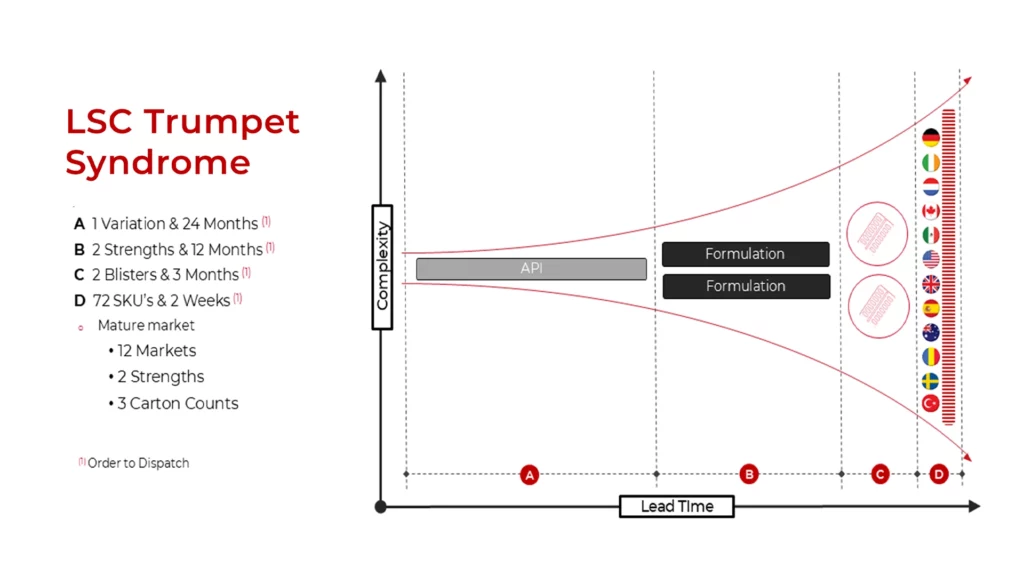
Levels of Late Stage Customization
Late Stage Customization can be implemented at various levels, depending on the company’s needs and investment capabilities. Each offers unique benefits such as flexibility, efficiency and cost reduction, but there are also considerations.
The four primary levels of LSC include:
Level 1 – Buy from Vendor
By ordering your digitally printed components directly from the vendor, there’s no capital investment required. Digital printing is a simpler process that requires less setup compared to traditional offset printing which results in quicker implementation, improved lead times and reduces operator exposure to challenging environments. This type of printing doesn’t require a minimum order quantity, which helps reduce the cost.
One consideration to keep in mind is thata material evaluation and stability testing may be required with this option. Initiating these activities early in the launch process will enable you to obtain Marketing acceptance of the digitally printed components, instead of trying to initiate their evaluation later in the process which could cause delays in the project timeline.
Level 2 – Inline Label Printing
This option requires investment in label printing equipment that would be installed on the packaging line but gives you more control over packaging operations and reduces component lead time since you aren’t relying on a vendor. By securing stock and storing it in-house, you’re able to bring these materials to the line as needed. Since labels are printed on demand in real-time there’s a substantial reduction in waste and greater flexibility than if you were to buy printed components directly from the vendor.
Just like with level 1, material evaluation and stability requirements need to be taken into consideration. In addition, a robust validation process is going to be critical in order to prove repeatability and confirm correct data on the printed components. Compared to level 1, the implementation time is longer due to securing equipment and completing the validation process.
Level 3 – Primary and Secondary Packaging Customization
If you have a large commercial product with many small, international SKUs, it may be beneficial to do primary and secondary in-line. This would include printing on top of blisters, labels, as well as secondary cartons. Level 3 enables less handling, which in turn provides a lower cost per unit since you don’t have to set up the line each time to run a new SKU. Eliminating pre-ordered components entirely and cutting dependency on external suppliers results in little to no waste, and accelerated turnaround times.
The same considerations apply to this level for material evaluation, stability requirements and robust validation. You’ll also need to factor in higher capital investment requirements for equipment, as well as longer implementation times compared to inline label printing.
Level 4 – High Volume, High Investment Full In-House Component Printing
Level 4 is the most advanced form of LSC where all components, including patient inserts, are printed in-house. While it requires the most investment, it provides the highest level of flexibility and cost efficiency. This option is ideal for rapid market launches and reducing time-to-market.
This option requires the most capital investment with additional printing capabilities, which demands more in-house expertise to run the operation. Robust validation and implementation times also need to be considered at this level of LSC.
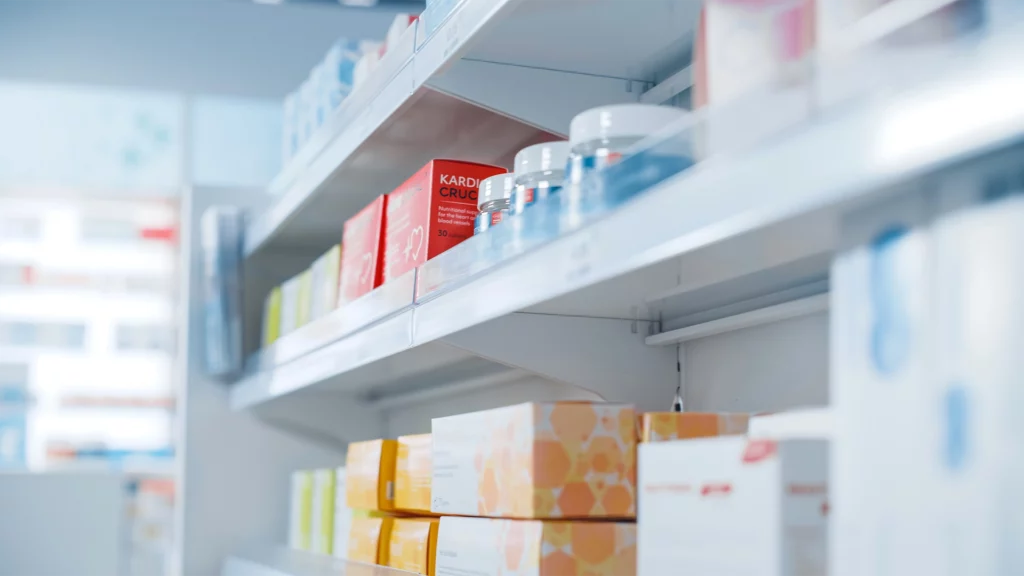
Financial and Operational Benefits
LSC minimizes lead times by eliminating dependence on pre-printed packaging components. By keeping stock in its lowest common denominator form (e.g., unlabeled blisters), companies can quickly react to changes relating to regulatory changes, forecast, and seasonality while improving working capital by not having costly expensive safety stock sat in a slow-moving market warehouse. It also helps streamline activities for drug products that have a shorter expiration date or limited stability data so you can get the product out the door quickly. These benefits not only apply to commercial products, but can help companies be strategic during clinical stages when exploring new indications for existing programs.
Traditional packaging often leads to excessive waste due to minimum order quantities, expired packaging stock, and redundant materials. LSC contributes to sustainability by reducing material waste, improving operational efficiency, and lowering the carbon footprint associated with transportation and logistics.
Overcoming Challenges in Late Stage Customization
While LSC presents numerous advantages, companies must address certain challenges to successfully implement this approach:
- Initial Capital Investment – Implementing Late Stage Customization, especially at higher levels, requires investment in digital printing equipment and workflow integration.
- Validation and Compliance – Companies must develop robust validation processes to ensure repeatability and regulatory compliance of printed components.
- Internal Expertise – Transitioning to LSC requires skilled personnel who can operate digital printing systems and manage new packaging workflows.
- Integration with Existing Systems – Companies must align LSC strategies with existing supply chain and ERP systems to ensure seamless operations.
The Future of Late Stage Customization in Pharma
As pharmaceutical packaging continues to evolve, Late Stage Customization is poised to become a standard practice across the industry. With advancements in digital printing technology and automation, companies can achieve greater efficiency, reduce costs, and improve their ability to meet market demands.
In the coming years, we can expect LSC to be further integrated with AI-driven forecasting tools, blockchain-enabled serialization, and on-demand manufacturing capabilities. The ability to personalize packaging at scale will redefine how pharmaceuticals are delivered, ensuring faster, more efficient, and more sustainable packaging solutions for global markets.
Conclusion
Late Stage Customization represents a transformative shift in pharmaceutical packaging, offering a highly adaptable and cost-effective solution for today’s complex supply chain challenges. By enabling just-in-time packaging, reducing waste, and improving compliance, LSC empowers pharmaceutical companies to stay ahead in a dynamic and competitive industry. As digital printing technology advances, the potential for LSC will only grow, making it a critical component of the future of pharmaceutical packaging.
This article was first published in Pharmaceutical Manufacturing and Packing Sourcer (PMPS) in April 2025
We are committed to supporting clients at every stage of the manufacturing cycle, delivering best-in-class services efficiently and effectively.
Find out more about our fully integrated Packaging Services.